INTEGRATED SYSTEM FOR PACKING AND TRANSPORT OF BITUMEN IN SOLID CONDITION
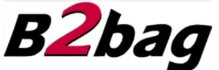
THE CHALLENGE
The world of today needs more bitumen: everywhere, anytime and at reasonable costs
Bitumen is one of the most important construction materials. It is used all around the world – in diferent climates and applications – mainly for road construccion. However, many countries or regions with ambitions road construction programmes can not be supplied with sufficent volumes at reasonable prices.
Bitumen production and marketing today faces a number of problemsw:
- Seasonality of consumption forces the producers to stop production in winter in the Norther Hemisphere.
- Demand peaks in the construction season cannot be covered.
- Demand peaks in the construction season can not be covered.cally (either filler in uneconomic metal drums or heated by a vast amount of energy e.g. in a Bitutainer TM).
- Bitumen can not be stored over an extended period without extensive and heating.
- Poor transportation logistics do not allow bitumen sale to all international customers.
BituBag ®: an integrated system for packing, storing and transport of bitumen in solid condition.
- The BituBag ® system is a complete logistic solution to make Bitumen available at any time and when it is most efficient and economic.
- To produce bitumen where and when it is most eifficient and economic.
- To supply bitumen where and when it is needed.
BituBag ®: solving the traditional problems of the bitumen industry.
THE MISSION
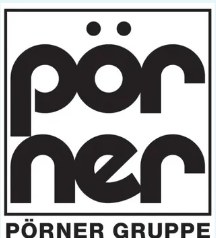
Pörner: the bitumen technology specialist.
The BituBag ® concept has been created and patented by Pöner, the leading bitumen technology company and majority shareholder of Bitumen Complete Solutions AG, both based in Vienna, Austria. Pörner offers bitumen processing plants for production of premium road paving bitumen as well as infrastructural units for storing, loading, packing and downstream processing.
In over 30 years of work in the field of bitumen the Pörner experts had to learn that in many regions bitumen supply was not economic. International bitumen tarde was hidered by the fact that no cheap and reliable packing system was available for long distance transportation and for storing. Traditionally bitumen is packed in metal drums made of thin steel sheets. In 1992, Pörner designed and supplied the world’s largest bitumen drum fabrication and filling unit with a capacity of 800 drums per hour. However, the metal drum system was recognized as too complicated, uneconomic and environmentally unfriendly for modern global trade, especially in the light of rising raw-material prices.
In 2002 Pörner started to develop a system for cooling and packing bitumen in large (i.e.750 – 1,000 kg) packing units, made from light plastic with optimum volume utilization.
BCS: a complete solution.
Pörner developed a new logistics solution, called BituBag ®, and founded Bitumen Complete Solutions AG (BCS), a company providing packaging services to bitumen producers, traders, transporters and the construction industry worldwide. With BituBag ®, BCS fulfils the mission of:
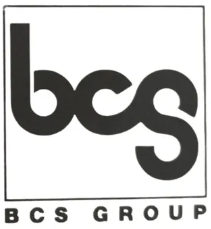
- Supply quality bitumen to all regions of the world.
- To countries that do not produce bitumen.
- Regions with underdeveloped logistics infrastructure.
- Developing countries.
- Take advantage of excellent crude resources by transferring the product to where the demand is.
- Enable bitumen producers to process, store and sell bitumen independently of seasonal variations.
- Ensure the cost-effective supply of all volumes of bitumen (from a few tonnes to hundreds or thousands).
BITUBAG ®: AN INTEGRATED SYSTEM
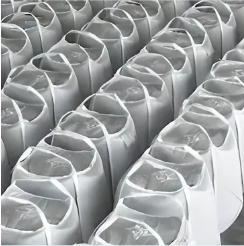
1. BituBag ®
The BituBag ® is a self-stabilising flexible container (patented by BCS AG). This bag is designed to transport up to 1000 kg of paving or industrial bitumen, taking into account both the viscoelastic properties during storage (in the solid state) and the transport conditions. It is suitable for filling in the liquid state at various temperatures and is made from a moulded plastic film. The volume of the bag, as well as its shape, are optimised for maximum loading on sea or road standad containers.
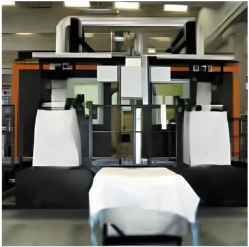
2. Bitumen cooling andd partitioning unit (CPU)
The CPU is used to fill the BituBag ®. The bitumen is cooled to a temperature slightly above the softening point andlower than the melting point of the plastic material of the container.
The unit has a filling capacity of 10 tonnes per hour and is operated by Bitumen Complete Solutions AG.
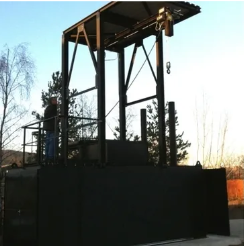
3. BituMelt bitumen melting unit
In this compact unit (which can be used on site, where bitumen is required), the contents of the bag are heated so that the bitumen becomes liquid again and reaches a temperature above the melting point of the plastic bag inside the BituBag. The units are powered by diesel at a rate of two tonnes per hour per unit (several units can operate in parallel).
LIFE CYCLE
- Reduced distribution costs per tonne of bitumen thanks to centralised industrial production of bags that meet BCS standards and quality control.
- Unlike conventional metal drums, it is possible to transport several thousand BituBags at a time to any location in the world easily and economically.
- The plasticBituBag ® is filled with bitumen at the cooling and conditioning unit (CPU). The filling temperature is controlled so precisely that the bitumen remains pumpable; it remains below the melting point of the plastic container, the BituBag, which also prevents the spread of noxious gases.
- Once filled, the bag is transferred to a storage area where it is left to cool at room temperature until the bitumen returns to a solid state.
- For long-distance transport, the bags can be placed in standard 6-metre containers. Stacking on two levels is possible to take advantage of the volume and capacity of the containers. With an average weight of 950 kg per sec, up to 19 tonnes can be loaded into a container.
- For local or regional transport, conventional trucks can be used. Based on European standards, it is possible to load 20 tonnes per layer.
- Bags of bitumen can be stored in any location, even outdoors if necessary, without heating, so that they can be sold at higher prices at the height of demand.
- Additional volumes of bitumen (produced during periods of inactivation, in winter, etc.) can be exported to foreign markets. BituBags are suitable for all long-distance transport mayens.
- Small or large quantities of bitumen can be transported over any distance, even to other continents, without heating and by any conventional vehicle..
- The solid bitumen is liquefied at low cost directly at its point of use using the BituMelt unit, which can be integrated into a hot preparation process.
- While the inner bag can be fused with bitumen, the outer bag can be used as a building material or recycled.
THE BITUBAG® SYSTEM
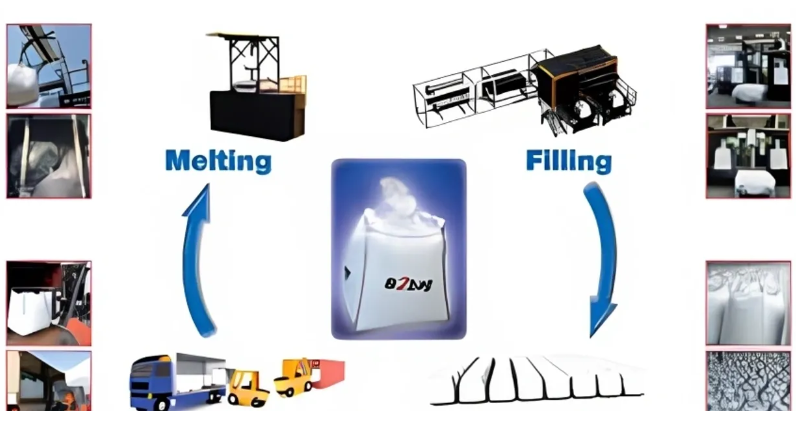
SYSTEM DESIGN
A design optimised for bitumen
- Transport of up to 1000 kg of bitumen for road paving at softening temperatures of 40 to 60 oC.
- Taking into account the viscoelastic properties of bitumen during storage and transport.
- Liquid filling at an optimised temperature (BCS AG patent).
Selection of materials
- Flexible plastic bag (polypropylene).
- Inner bag made of thermoplastic film (polyethylene).
- Resistant to rain and ultraviolet radiation.
Weight – Volume – Shape
- Minimum size of the entire bag system.
- Maximum net volume thanks to optimised dimensions.
- Stabilised shape thanks to self-tensioning system.
- Bag compatible with international container and lorry dimensions.
Stability and safety
- Designed and certified for transport of viscous liquids.
- Classification as non-hazardous (cold bitumen).
Environmental features
- Inner liner bag material is melted and therefore integrated with the bitumen at final application.
- No heating energy is required during the storage and transport process.
- Used outer bag material can be used as construction material (fabric for soil stabilization) or economically recycled.
Handling
- Empty: easy supply and transport of folded empty bags.
- Dilled: handling by forklift truck and trasnport possible on open trucks, rail waggons, barges, ships in closed containers or any other conventional means of transportation.
BITUBAG ® SPECIFICATIONS
The BituBag ® is a flexible, self-stabilising plastic bag specially optimised for loading into 6-metre containers and onto lorries.
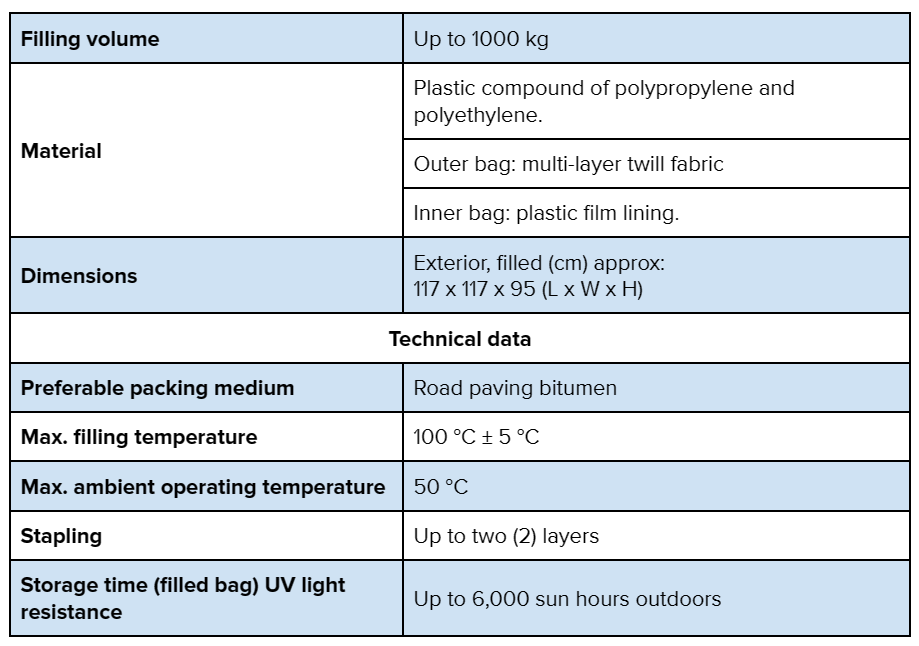
Handling of the BituBag ®
Once filled, the BituBag ® can be manoeuvred using the top handles (using a forklift truck). It can be moved at any temperature, even immediately after filling when the bitumen is still in a liquid state.

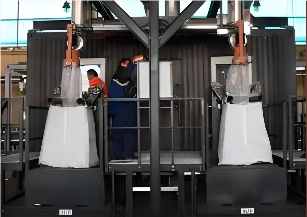
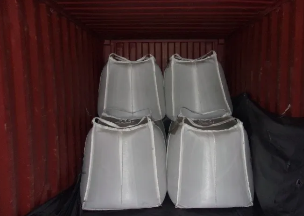
IMPLEMENTATION AND OPERATION
BCS at the origin of a new form of bitumen distribution
BCS is the patent holder of the BituBag ®, which is much more than a large self-stabilising plastic bag for transporting viscous bitumen used in road construction. The result of years of research, the BituBag ® is a complete logistics system offering unrivalled properties to the bitumen industry. BCS’s comprehensive range of services includes packaging, transport and storage of bitumen in solid form.
The first steps
Following a preliminary study that takes into account the economic and commercial environment and the existing infrastructure, BCS installs the required equipment (CPU cooling and conditioning unit and/or BituMelt) on site. The customer supplies only the bitumen.
Operation of the BituBag ® system
- BCS offers complete conditioning and logistics services.
- BCS installs and operates the BituBag ® cooling and conditioning unit (<<CPU>>, which remains the property of BCS).
- BCS produces and supplies the BituBags.
- BCS charges a fixed price per tonne of BituBag ® packaging.
- BCS operates and maintains the CPU unit with a high level of availability.
With BCS, the world of bitumen is yours
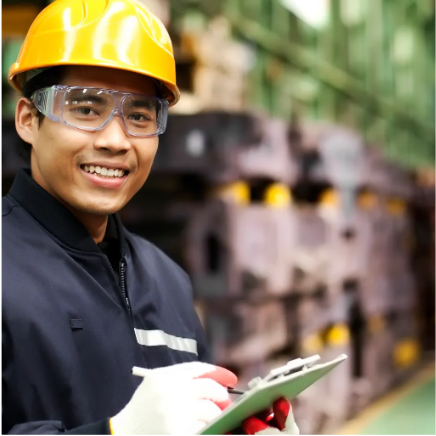
BCS AND PÖRNER: THE BITUMEN EXPERTS
BCS at the origin of a new form of bitumen distribution
Pörner is the technological leader in the production and conditioning of bitumen, with licences and operating contracts for more than 30 Biturox processing plants worldwide, as well as conditioning and filling plants for trucks, railways and metal drums.
Biturox bitumen plants
- BP Laverda Refinery, France
- PKN Plock Refinery, Poland
- LINOS, Lisichansk Refinery, Ukraine
- Mobile Adelaide Refinery, Australia
- CPC Refinary, Kaohsiung, India
- Azerneftiang Reinery, Baku Aszerbaidjan
- Jarbit Bitumen, Jaroslavl, Russia
- CHEL, Chelavtodor, Chelyabinsk, Russia
BituFil – bitumen filling facilities
- Ufaneftechim Rafinery, Ufa, Russia
- MPE Yangoon Refinery, Myanmar
- Simosa Oil Co. Mailiao, Taiwan
- MOL Szazhalombatta Refinery, Hungary
DrumFil – bitumen filling facilities
- NIOC Esfaham Refinery, Iran
- NIOC Banar Abbas Refinery, Iran
- Thai Petrochemical (TPI) Rayong, Thailand
BituBag ® – flexible container filling plant
- MPE Yangoon Refinery, Myanmar
- BCS Jurong, Singapore
- Petrogal Refinery, Porto, Portugal
- MBW Bitumen Works, Leeipzig, Germany
BCS AG is a 75%-owned subsidiary of the Pörner Group. SBA AG, a 100% subsidiary of BCS AG, builds and assembles the CPU and BituMelt units.